Shrinking manufacturing’s carbon footprint
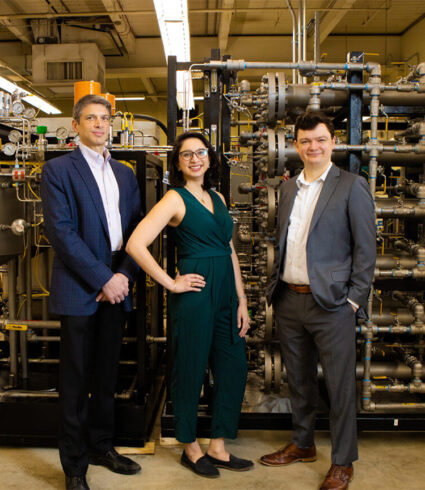
What it does
Via Separations, headquartered in Watertown, Massachusetts, uses a type of strainer to separate chemicals, an important step in manufacturing everything from cardboard boxes to sneakers. Graphene oxide, essentially chemically treated pencil lead, is used as a filtration method.
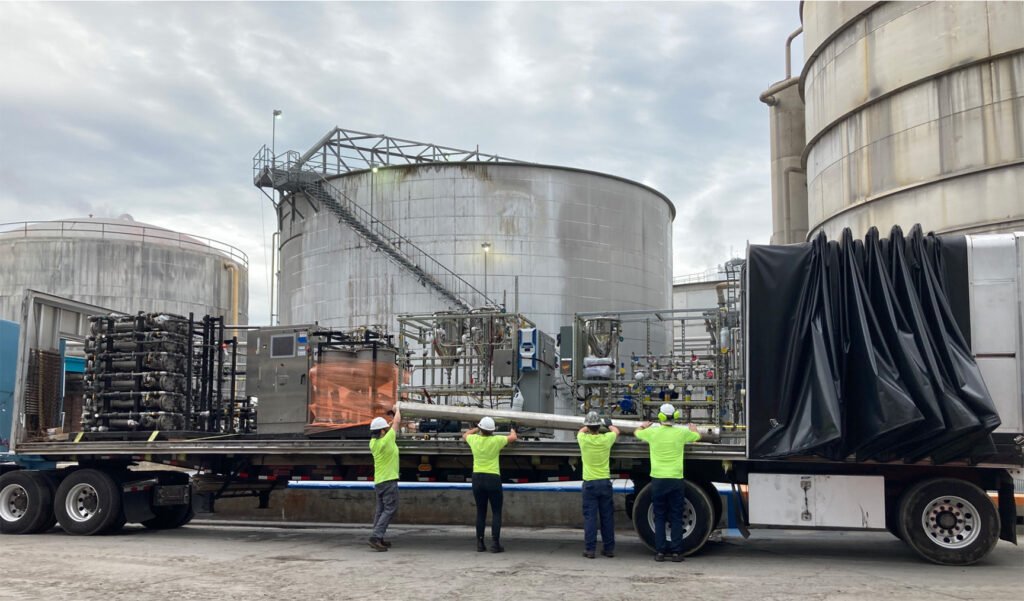
a customer site. Photo: Courtesy of Via Separations
Why it matters
Most products today have what’s called “embodied carbon,” says Shreya Dave, co-founder and CEO at Via Separations. “That’s the carbon or the resources that have gone into the production of it.” Think of the rubber in shoes or plastic in office chairs. To produce those materials, manufacturers need to separate chemical compounds from one another. They do that using evaporation and distilling methods. That uses up a lot of energy—equivalent to 12% of US energy consumption.
Via Separations uses membrane technology to separate chemicals, saving energy and resources in the process. “We deposit layers of graphene oxide onto a substrate to make the membrane,” said Brent Keller, co-founder and chief technology officer.
Take the pulp and paper industry as an example. “For every pound of cardboard that becomes a box there’s about two pounds of everything else that was in the tree,” Keller said. “What we do is use that membrane to directly press water out of that mixture, so that we can concentrate it without needing nearly as much energy, about 80% to 90% less.”
Via Separations’ technology uses 80% to 90% less energy than traditional methods.
How it started
Via Separations has its roots in Dave’s PhD research at MIT with DMSE’s Jeffrey Grossman, the Morton and Claire Goulder and Family Professor in Environmental Systems. Dave focused on making better membrane materials for water filters. But the economics of selling new water filtration technology didn’t make sense. “There wasn’t a dollar-and-cents reason for folks to transfer over,” said Dave. Chemical separation, in contrast, offers a huge opportunity for cost savings. “And the added benefit is the decarbonization.”
Dave linked up with Keller, another DMSE grad, to establish Via Separations. Grossman serves as chief scientist.
What’s next
In 2022, Via Separations was awarded a $9.75 million grant from the Department of Energy’s ARPA-E, an agency designed to commercialize breakthrough technologies for emissions impact. The team is building its first commercial system, to a pulp and paper company. After scaling sales in that industry, the company plans to expand to plastics, construction materials, and fertilizers.
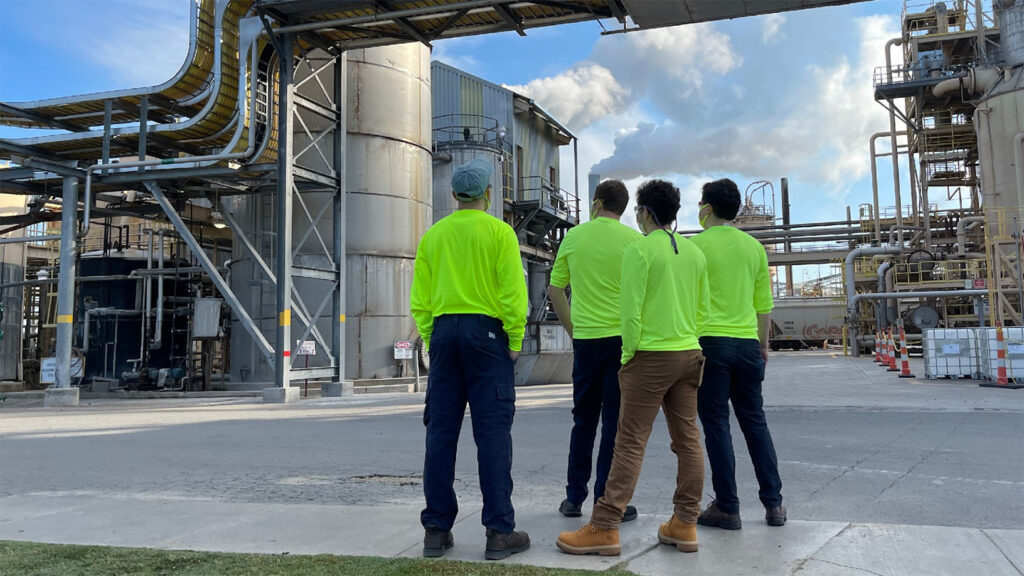