DMSE undergrads take first in annual materials design competition
Two MIT undergrads got a winning start to their senior year by taking the top spot—and $2,000 in prize money to share—in the annual ASM Materials Education Foundation’s 2023 Undergraduate Design Competition. Louise Anderfaas and Darsh Grewal, students in Professor Gregory Olson’s 3.041 (Computational Materials Design), worked with MIT postdoc mentor Margianna Tzini on the complex project.
“This is probably the highest level of complexity that an undergraduate team has undertaken,” says Olson, who came to MIT from Northwestern University in 2020. He has supervised teams in the contest at both schools. Last year MIT took third place for designing a 3-D printable alloy for stamping out Tesla parts.
ASM Materials Education Foundation is the charitable division of materials engineering organization ASM International. It promotes applied science careers to students and teachers.
Super-strong and affordable
Anderfaas and Grewal’s winning project was about creating a super-strong aluminum plate, 10 centimeters thick, for use in applications like planes and cars. It was critical that the material be very tough, resisting things like stress corrosion and fractures. They made a video to explain their step-by-step process, using computer models and calculations to figure out the best combination of materials and design.
“For the material to be affordable and to be used in industrial applications, we used conventional processing roots,” Anderfaas says, referring to traditional manufacturing methods such as cutting and milling rather than more cutting-edge techniques, which offer improved performance and other benefits but are often more expensive. “But in order to be used in airplanes, we had to make a large-scale product.”
Anderfaas and partner Grewal, both seniors in the Department of Materials Science and Engineering (DMSE), had just three months to integrate all these properties and use computational tools to accelerate their design.
The ultra-high strength aluminum plate alloy satisfies real-life property requirements provided by the DSO National Laboratory in Singapore, which collaborated with MIT on the project. To develop a material that was strong and flexible and could withstand stress without corroding, the students used computational tools based on CALPHAD, a method for calculating the properties of materials, and incorporated density functional theory (DFT) data. DFT data provides insights into the electronic structure of the material, aiding in the optimization of its properties.
The team used multi-objective optimization, which was key in balancing the necessary variables. “When you try to design something, internally, there is always a cost. When you try to increase the strength, you’re losing something else,” recalls Grewal. Making something stronger might make it less flexible, for example. So instead of focusing on individual properties, “we treated the system as a whole.”
Anderfaas and Grewal cited the classic hierarchical approach to materials design that Olson teaches during his classes. “It goes in two ways, both the structure affects the properties, and the properties affect your structure,” says Grewal. “You have to understand this relationship.”
The challenge: There are lots of relationships to distinguish in a complex problem. “You have to distinguish which are the important parts, and how all these parts are related and connected to each other,” adds Grewal.
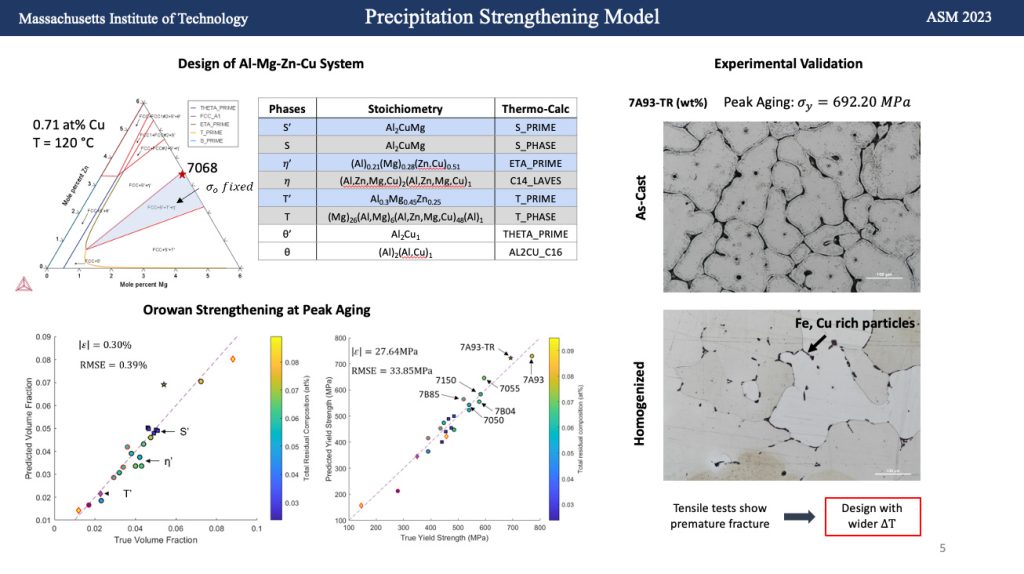
Anatomy of computational design
Olson’s class breaks new ground in a field he helped invent: the computational design of new materials. The class brings together core concepts from the MIT materials science curriculum—thermodynamics, kinetics, and mechanical properties, for instance—and teaches students how to design materials by developing an understanding of the process-structure-property-performance relationships that define material behavior. The class culminates with a final design project—the subject matter of the competition—in which student teams design a novel material that addresses current practical material challenges.
“I’ve devoted my research career to this technology and its commercialization,” says Olson, the Thermo-Calc Professor of the Practice for DMSE. Through his startup, QuesTek, the technology has been adopted by industry giants including Apple, SpaceX, and Tesla. “Those companies tend to be very interested in the students who take my class and typically offer internships and some permanent positions.”
The class is organized into team projects drawn from funded graduate research, so grad students and postdocs can serve as the coaches to the student teams, allowing them to go to a much higher technical level than would otherwise be possible, says Olson. Tzini guided the students with specific details about the project and helped them distinguish the different aspects and then connect them.
The databases the students used for the project are aligned with the Materials Genome Initiative, a US government initiative aimed at accelerating the discovery and development of new materials. They include information on the properties, structures, and behaviors of a huge assortment of materials. The same way the human genome serves as a database that directs the assembly of structures of life, here the materials genome contains equally fundamental data that can be used to direct the assembly of a multiscale microstructure of a material that evolves throughout sequential stages of processing.
“So the databases are allowing us to take the mechanistic knowledge we have and apply it in a quantitative systems-specific way. The class really integrates the whole curriculum of the undergraduate materials program in those design projects,” Olson says. He’s proud to see students like Anderfaas and Grewal having success with the subject matter.
The students were surprised but pleased by their ASM competition win. “Grasping all of these concepts and balancing everything was difficult,” says Grewal. “This is definitely the hardest class I’ve taken but also the most rewarding.”
Second prize in the competition went to Purdue University for improving the process of flattening forged aluminum components, and third prize went to Michigan Technological University for reducing the presence of boron impurities when making cast iron from recycled steel.